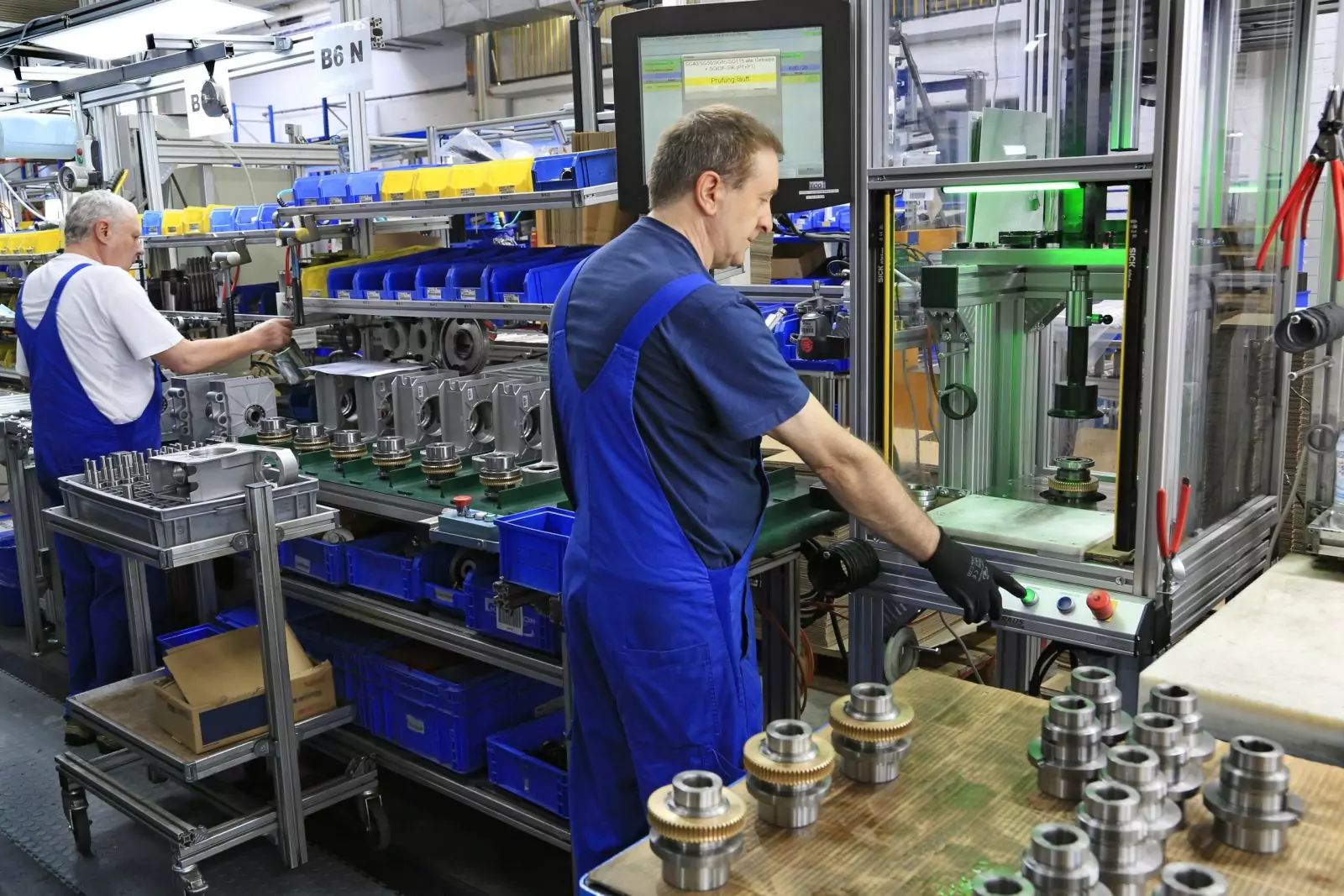
25 jan Servo-persen werken nauwkeurig, schoon en met procesbetrouwbaarheid
Elektrische persen met kracht- en trajectbewaking en een nauwkeurigheid van een honderdste van een millimeter
De poortaandrijvingsfabrikant GfA heeft zijn hydraulische persen vervangen. In plaats daarvan monteren elektrische persspindels van Atlas Copco Tools nu transmissies. Ze persen schoon, veilig en met volledige traceerbaarheid.
Bij de assemblage van transmissieonderdelen is het persen een traditioneel en nog steeds onmisbaar verbindingsproces. Omdat de toegepaste kracht kan worden gebruikt om een grote verscheidenheid aan componenten permanent te verbinden, zijn er in bijna elke industrie perstoepassingen te vinden. Dit is ook het geval bij de poortaandrijvingsfabrikant GfA ELEKTROMATEN GmbH & Co. KG uit Düsseldorf. Het bedrijf drukt onder andere wormwielen en kogellagers op de holle assen van de tandwielkasten voor zijn ongeveer 5000 verschillende aandrijvingsvarianten.
“Vorig jaar hebben we onze productie opnieuw afgestemd op de standaarden van Industry 4.0 en sindsdien hebben we de modelgerelateerde exacte persing van de componenten aangevuld met de automatische en verifieerbare documentatie van de parameters perskracht en trajectlengte”, meldt het hoofd van de assemblage bij GfA, Willi Hanen.
Het verbindingsproces wordt gestart door het scannen van een barcode en een volledig nieuw type pers, waarna de benodigde parameters voor het betreffende onderdeel worden opgevraagd. Zodra de medewerker de met de hand voorgemonteerde onderdelen in het werkgebied van de spindel plaatst, die door een lichtgordijn wordt beschermd, worden de onderdelen met een druk op de knop met de grootste precisie samengedrukt. Het aandrukken van de wormwielen en lagers is een belangrijke montagestap, maar GfA zou zijn vorige hydraulische persen alleen aan de nieuwe eisen hebben kunnen aanpassen met een zeer hoge ombouw- en retrofit-inspanning. In plaats van de hydraulische machines om te vormen tot intelligent in een netwerk opgenomen en voor gegevens geschikte perssystemen met extra meetsystemen en speciale software, koos Hanen voor een “dynamische oplossing met genen uit de moderne schroeftechniek”: In eerste instantie installeerde het bedrijf uit Düsseldorf bij wijze van proef een PST-unit van Atlas Copco Tools als alternatief voor de hydraulische persen. Deze servo-pers beloofde een hogere precisie, meer proceszekerheid en, met perssnelheden tot 500 mm/s (millimeter/seconde), een grote snelheid en tijdsbesparing. “Het feit dat het ook niet meer nodig was om olie en filters te vervangen vanwege de schone, zuiver elektrische werking, was een extra milieuvriendelijk aspect”, zegt de montagebegeleider gelukkig.
Lineaire extensie
Het hart van de PST is een gemodificeerde elektroschroefspindel uit de QST-serie, die zich al vele duizenden keren heeft bewezen in assemblagesystemen voor veiligheidskritische en documentair vereiste schroefverbindingen. Het verschil met de schroevendraaiende versies is dat de PST-spindels de rotatie omzetten in een lineaire beweging, die ze in de axiale richting overbrengen via een planetaire rolspindel. Op deze manier hebben de Zweden het werkingsprincipe van een elektrisch schroevendraaiersysteem, dat het koppel en de aanhaalhoek nauwkeurig regelt en bewaakt, in de lineaire richting uitgebreid tot de parameters van de traject en kracht.
Kracht-trajectsmonitoring – robuust en toch gevoelig
Willi Hanen benadrukt dat een PST-servopers de perskracht op een uiterst nauwkeurig gedoseerde manier toepast. Het is net zo belangrijk voor het optimaal functioneren van de tandwielkasten dat de diepteparameters behouden blijven. Hier komt het gebruikersvriendelijke elektrische alternatief pas echt tot zijn recht: “We kunnen de persdiepte van de PST tot op een honderdste van een millimeter nauwkeurig instellen en de meetsensoren van de elektrische spindel zijn uiterst gevoelig. De productie bij GfA heeft hier een waardevol concreet voordeel bij. Want als er bijvoorbeeld een storend onderdeel tussen de te verbinden onderdelen zou komen, zou de opgegeven drukafstand zelfs met maximale perskracht niet volledig worden bereikt. “Volgens onze praktijkervaring detecteert de gevoelige elektronica dergelijke kleine afwijkingen absoluut betrouwbaar en stopt het verbindingsproces!
Pas na de juiste correctie en controle – door het perssysteem zelf – wordt het onderdeel vrijgegeven. En pas dan wordt het onderdeel, dat zo gedocumenteerd is dat het niet te verwarren is, met de lagers en wormwielen optimaal op de holle as in het tandwielkasthuis geplaatst en vrijgegeven voor de verdere afwerking, terwijl een nieuw scanproces al begint met het volgende persproces.
Tijdens het persproces zelf registreert het PowerMACS 4000 PST-besturingssysteem de verbindingsgegevens, documenteert ze op een traceerbare manier en stuurt ze via Open Protocol door naar het Enterprise Resource Planning System (ERP) van GfA. “Via deze gesloten keten van data-opslag verzamelen we alle kwaliteitsrelevante informatie om deze te analyseren en bruikbaar te maken”, bevestigt de montagebegeleider. “Tegelijkertijd was de integratie vrij eenvoudig en is er geen extra hardware of software nodig voor de volledige integratie van de persen in ons bestaande systeem”, erkent Hanen. Bovendien is er volledige compatibiliteit met het ToolsNet diagnoseprogramma van Atlas Copco, dat aanvullende gedetailleerde rapporten en diagnostische gegevens voor de schroeftechnologie mogelijk maakt die verder gaan dan de analyse van de persresultaten.
Betere kwaliteit door traceerbaarheid van alle persgegevens
“Door de gegevens samen te voegen met de serienummers en foto’s van de samengevoegde onderdelen kunnen we bij alle montagestappen betrouwbaar bewijzen dat onze transmissies volgens de specificaties zijn vervaardigd. De evaluatie van de via het PST-systeem verkregen assemblagegegevens is echter minstens zo belangrijk voor Hanen: “Hierdoor kunnen we onze processen verder optimaliseren en wordt herbewerking geëlimineerd”.
Vanuit het oogpunt van Hanen brengen de modulaire PST-systemen met krachttrajectbewaking nog meer voordelen met zich mee voor het montageproces: “Terwijl wij met deze flexibele apparaten onze extreem hoge variaties van de tandwielkasten perfect in kaart kunnen brengen, geven de PST’s onze medewerkers op elk moment door middel van visuele signalen informatie over de processtatus en leiden ze zo door het hele verbindingsproces. Bovendien zijn PST’s met 70 dB/a zeer stil en tot 90 procent energiezuiniger dan hun hydraulische voorgangers. Dit is nog een reden waarom we nu alle vier de transmissielijnen hebben uitgerust met deze persen die tot 100 kN (kilonewton, gelijk aan ongeveer 10 ton) sterk zijn”.
„Kwaliteit is onze drijfveer“
GfA ELEKTROMATEN GmbH & Co. KG is leverancier van aandrijfsystemen voor industriële poorten. Opgericht in 1954, werken vandaag de dag ongeveer 250 medewerkers op de vestiging in Düsseldorf. Onder de merknaam ELEKTROMATEN® verkoopt het bedrijf wereldwijd meer dan 200.000 aandrijvingen en 150.000 deurbesturingen per jaar. Het assortiment wordt aangevuld met een uitgebreid accessoireprogramma. De hoogwaardige producten worden binnen enkele dagen in meer dan 5.000 varianten op bestelling gemaakt, specifiek voor de bouwplaats in gebruik genomen en wereldwijd geleverd. Dit wordt bereikt door middel van een modern, computergestuurd machinepark, een uitgekiend logistiek concept en diverse arbeidersgeleidingssystemen in de productie, montage en verzending.