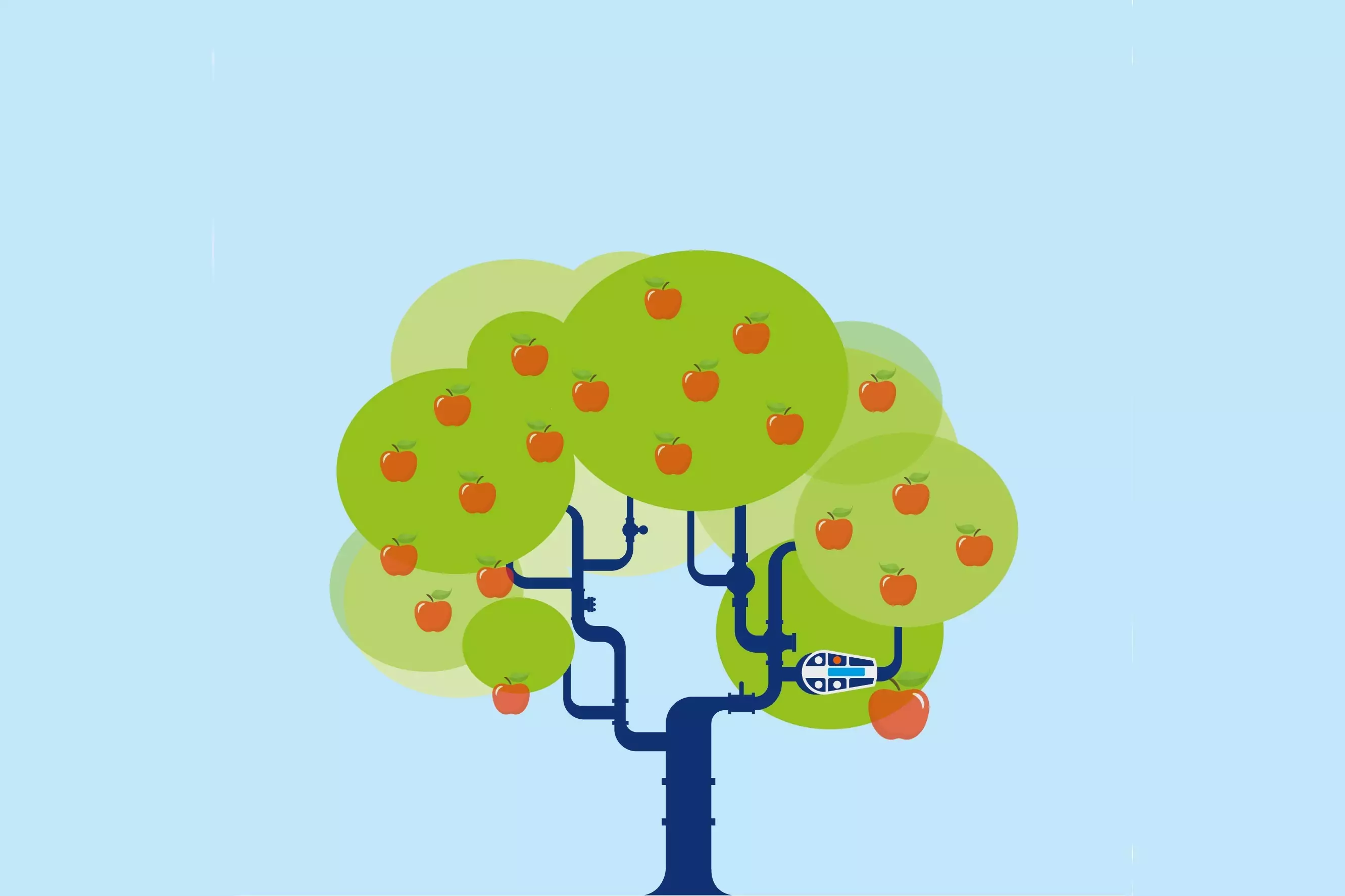
03 okt Technieken en methodes voor het optimaliseren van persluchtsystemen
Beheersing van persluchtlekkages
Perslucht is in veel fabrieken een onmisbare energiedrager. Maar ook een dure! Desondanks gaan veel bedrijven slecht met hun persluchtsysteem om. Vaak worden lekkages en drukval genegeerd, wat samen met een verkeerd compressorgebruik en/of een te hoge systeemdruk resulteert in extreem hoge energiekosten. Daarnaast is er het verhoogde risico van productiestilstand omdat door inefficiënties, lekkages en drukval ook de back-up compressor vaak vol in bedrijf is. Er zijn makkelijke en relatief goedkope lekkage managementtechnieken om het energetische rendement van een persluchtinstallatie snel te verhogen. Vervolgens kan men verschillende meet-, analyse- en monitoringsystemen inzetten om het totale persluchtsysteem duurzaam te optimaliseren.
In dit artikel gaan we in op methodes en technieken om het rendement van een persluchtinstallatie zowel op korte als lange termijn te verhogen. We starten daarbij met wat ‘het laaghangende fruit’ van persluchtinstallaties genoemd wordt. Dit is het opsporen en verhelpen van lekkages waardoor het energieverlies en dus ook de kosten snel met vele procenten tegelijk omlaaggaan. Voor het identificeren en kwantificeren van lekkages zijn verschillende methodes beschikbaar. Er zijn simpele methodes die al vrij snel een grove indicatie van het lekkageniveau opleveren. Wil men er serieuzer mee aan de slag, dan zijn lekdetectoren en flowmeters nodig alsmede een financieel budget en mankracht voor het uitvoeren van de lekdetecties en de reparaties. Het repareren van lekkages is echter heel lonend. Ten eerste in financieel opzicht omdat ondernemingen hun kosten onmiddellijk zien dalen. Ten tweede merken de mensen op de werkvloer dat een beter presterend persluchtsysteem de kans op productiestoringen verkleint, wat motiverend werkt.
Snel een indruk van de lekkage-omvang
Het is een van de oudste maar tegelijkertijd ook een van de eenvoudigste en snelste methodes om een indicatie te krijgen van de aanwezigheid van lekkages in het persluchtsysteem. Wat u hiervoor moet doen is simpelweg de tijd te meten (in minuten) van respectievelijk de laadtijd (T1) en ontlaadtijd (T2) van de compressor. Vervolgens kan met de volgende formule eenvoudig het lekpercentage worden berekend:
Totaal lekpercentage (%) = [(T1*100)] / [(T1+T2)]
Bij een uitkomst hoger dan 10% kan men ervan uitgaan dat er in de fabriek duidelijk sprake is van persluchtlekkage. Een andere en eveneens beproefde en snelle methode om dit te verifiëren is de drukvaltest. Deze test moet net als de eerste test worden uitgevoerd als de fabriek stilligt. In theorie wordt er dan in feite geen perslucht verbruikt. Slaat de compressor toch geregeld aan, dan kan men ervan op aan dat er sprake is van lekkages. Hoe groot die zijn kan men min of meer inschatten door, nadat de compressor het complete persluchtsysteem op de werkdruk heeft gebracht, de compressor uit te zetten en naast de drukmeter te gaan staan met een stopwatch. Vervolgens wordt de tijd gemeten die het systeem nodig heeft om 1 of 2 bar in druk te dalen. Hoe sneller dit gaat des te groter is het aantal cq. de omvang van de lekkages. Los van het feit dat bij beide tests de fabriek stilgelegd moet worden is een ander nadeel dat er bij deze metingen geen rekening wordt gehouden met de inefficiëntie van de compressor zelf. Want ook al lijkt de compressor normaal te werken kan er (vooral bij oudere compressoren) sprake zijn van slijtage en inwendige lekkages. Ook geven beide methodes geen informatie over de specifieke locatie van lekken in het persluchtsysteem en zijn deze tests niet geschikt voor fabrieken die 24/7 in bedrijf zijn vanwege de noodzakelijke stop. Voordeel is echter dat beide tests geen financiële investeringen vergen.
Ultrasoon lekdetectie
Nadat met bovenstaande ‘snelle methodes’ is geconstateerd dat er daadwerkelijk sprake is van serieuze persluchtlekkage, is het zaak de exacte locatie en grootte van alle lekken zo snel mogelijk in kaart te brengen. Dit kan met gebruikmaking van bijvoorbeeld ultrasoon lekdetectoren. Deze zijn in staat elk lek op te sporen, dus ook de lekken waarvan het geluid buiten het bereik van het menselijk gehoor ligt. Weliswaar vergt de aanschaf van een ultrasoon detector een zekere investering, maar deze wordt door de gerealiseerde besparing heel snel terugverdiend. Met ultrasoon lekdetectiesystemen kan niet alleen de locatie van een lek, maar ook de mate van lekkage in beeld worden gebracht. Vervolgens kan men voor ieder lek uitrekenen hoe groot het financiële verlies is en kan men op basis van de reparatiekosten de ‘return on investment’ (ROI) berekenen. De lekkages met de grootste ROI kan men dan als eerste aanpakken waardoor sneller significante besparingen worden gerealiseerd.
Lekkage management op basis van data met flow monitoring
Een gedegen methode om serieus met lekkage management aan de slag te gaan, is het gebruik van flowmeters. Men kan een of meerdere flowmeters in het persluchtnetwerk installeren. Dat kan bijvoorbeeld in de hoofdleiding na de buffertank, maar ook in hoofdleidingen per productieafdeling. Dit laatste is nuttig omdat dit niet alleen een beeld geeft van het persluchtverbruik maar ook van het lekkageniveau per afdeling. Op basis van de uitkomst kan men vervolgens gerichter aan de slag met lekdetectie. Monteert men flowmeters voorafgaand aan het repareren van lekkages, dan heeft men na de lekkage-reparaties direct een duidelijk beeld van de hierdoor bereikte besparing. De nieuwe gemeten waarde van het totale verbruik is dan meteen het nieuwe ‘basisverbruik’. Stijgt het persluchtverbruik ten opzichte van dit nieuwe uitgangspunt zonder dat hier vanuit de productie aanleiding toe is, dan kan dit wijzen op nieuwe lekkages. Hoe meer flowmeters er in de fabriek geïnstalleerd zijn, des te gerichter kan men bepalen op welke locatie sprake is van afwijkende toenames. Dit deel kan vervolgens met ultrasoon detectoren worden onderzocht op lekkages. Door het continu monitoren van het persluchtverbruik vallen (grote) lekkages direct op en kunnen deze onmiddellijk verholpen worden waardoor wordt voorkomen dat deze over langere termijn hoge kosten veroorzaken. Altijd zullen er echter nieuwe lekken ontstaan en door deze in een vroeg stadium te ontdekken en te verhelpen beperkt men lekkageverliezen tot een minimum. Als alle lekkages zijn ‘gesaneerd’ kan men de frequentie van lekdetecties langzaam terugschroeven. Onnodige lekdetectierondes (en kosten) worden daarmee voorkomen. Uiteindelijk zijn met deze gecombineerde aanpak besparingen op het overall energiegebruik realiseerbaar van 10 tot 30%. Geadviseerd wordt om wel flowmeters te gebruiken die naast flow, ook druk, temperatuur en totaalflow meten. Met 4-in-1 flowmeters kunnen grotere optimalisaties gerealiseerd worden.
Bi-directionele flow of een lek?
Wordt vermoed dat er sprake is van lekkages, houdt er dan rekening mee dat er sprake kan zijn van afwijkende systeemgedragingen zoals bijvoorbeeld bi-directionele flow. Dit houdt in dat lucht onverwachts in tegenovergestelde richting door het systeem beweegt. Dat wekt de schijn van persluchtverlies (lekkage), terwijl dit dus niet aan de orde is. Is het systeem voorzien van bi-directionele flowmeters, dan kan men dit onmiddellijk zien. Ook is het van cruciaal belang om kritisch te kijken naar de systeemdruk. Des te hoger de druk, des te meer perslucht zal er immers verdwijnen via lekkages. Een lagere systeemdruk is bovendien niet alleen om deze reden interessant want elke bar drukverlaging resulteert namelijk ook in 7% energiebesparing!
Perslucht- en energiemonitoring
Los van lekkages zijn er vele andere factoren die het rendement van persluchtsystemen kunnen verlagen. Monitoring, met gebruikmaking van vermogens-, flow-, druk-, temperatuur- en dauwpuntsensoren, geeft zowel kwalitatieve als kwantitatieve informatie over het totale persluchtsysteem inclusief compressor(en), drogers en filters. Bij toepassing van bijvoorbeeld een VPVision real-time monitoringsysteem worden systeem gegevens opgeslagen en kunnen trends eenvoudig worden ontdekt. Deze worden o.a. gevisualiseerd via het dashboard en/of in rapporten waardoor men een helder beeld krijgt van (het verloop van) de systeemprestaties. De gegevens worden real-time gemonitord, waarbij analyses ook real-time uitgevoerd kunnen worden. Monitoring is dus ook en misschien wel juist geschikt voor toepassing in 24/7 fabrieken.
Bij een uitgebreide persluchtmonitoring wordt ook het energiegebruik van grootverbruikers als compressoren gemeten (energiemonitoring). Hierbij kunnen periodiek waardevolle energiemanagementrapporten worden gegenereerd waardoor het verbruiksniveau over langere periodes zichtbaar wordt. Is sprake van afwijkingen van het gemiddelde gebruik dan is dit een signaal om te onderzoeken wat daarvan de oorzaak is. Door na genomen maatregelen zoals het repareren van lekken het energiegebruik te blijven monitoren houdt men de vinger aan de pols. Bij afwijkingen kan men tijdig ingrijpen en ook kan men na genomen acties, zoals drukverlaging en/of lekreparaties, exact in de gaten houden wat daarvan het effect is. Dit legt de basis voor een duurzaam, economisch en in alle opzichten optimaal presterend persluchtsysteem.